Introduction
Paper Packaging History
A wide range of paper and paperboard is used in packaging today – from lightweight infusible tissues for tea and coffee bags to heavy duty boards used in distribution. Paper and paperboard are found wherever products are produced, distributed, marketed and used, and account for about one-third of the total packaging market. Over 40% of all paper and paperboard consumption in Europe is used for packaging and over 50% of the paper and paperboard used for packaging is used by the food industry.
One of the earliest references to the use of paper for packaging food products is a patent taken out by Charles Hildeyerd on 16 February 1665 for ‘The way and art of making blew paper used by sugar-bakers and others’ (Hills, 1988).
The use of paper and paperboard for packaging purposes accelerated during the latter part of the nineteenth century to meet the needs of manufacturing industry. The manufacture of paper had progressed from a laborious manual operation, one sheet at a time, to continuous high speed production with wood pulp replacing rags as the main raw material. There were also developments in the techniques for printing and converting these materials into packaging containers.
Modern Paper Packaging
Today, examples of the use of paper and paperboard packaging for food can be found in many places, such as supermarkets, traditional markets and retail stores, mail order, fast food, dispensing machines, pharmacies, and in hospital, catering and leisure situations.
Uses can be found in packaging all the main categories of food, such as:
- Uses can be found in packaging all the main categories of food, such as:
- dry food products packaging – cereals, biscuits, bread and baked products, tea, coffee, sugar, flour, dry food mixes, etc
- frozen foods, chilled foods and ice cream packaging
- liquid foods and beverages – juice drinks, milk and milk derived products
- chocolate packaging and sugar confectionery
- fast foods
- fresh produce – fruit, vegetables, meat and fish
Packaging made from paper and paperboard is found at the point of sale (primary packs), in storage and for distribution (secondary packaging).
Fibers
Paper and paperboard are sheet materials made up from an interlaced network of cellulose fibers. These materials are printable and have physical properties that enable them to be made into flexible and rigid packaging by cutting, creasing, folding, forming, gluing, etc.
There are many different types of paper and paperboard. They vary in appearance, strength and many other properties depending on the type(s) and amount of fibre used and how the fibres are processed in paper and paperboard manufacture.
GSM
The amount of fiber is expressed by the weight per unit area (grams per square metre, g/m2, or lbs per 1000 sq ft), thickness (microns, mm or 0.001 mm, and thou (0.001 inch), also referred to as points) and appearance (color and surface finish).
Difference Between Paper and Paperboard
Paperboard is thicker than paper and has a higher weight per unit area. Paper over 200g/m2 is defined by ISO (International Organisation for Standardization) as paperboard or board. However, some products are known as paperboard even though they are manufactured in grammages less than 200g/m2.
Paper Packaging Categories
Papers and paperboard used for packaging range from thin tissues to thick boards. The main examples of paper- and paperboard-based packaging are:
- custom paper bags, wrapping, packaging papers and infusible tissues, e.g. tea and coffee bags, sachets, pouches, overwrapping paper, sugar and flour bags, carrier bags
- multiwall paper sacks
- folding cartons and rigid paper boxes
- corrugated boxes and solid fiberboard boxes (shipping cases)
- paper-based tubes, tubs and composite containers
- fiber drums
- liquid packaging
- molded pulp containers
- labels
- sealing tapes
- cushioning materials
- cap liners (sealing wads) and diaphragms (membranes)
Paper and paperboard packaging is used over a wide temperature range, from frozen food storage to the high temperatures of boiling water and heating in microwave and conventional radiant heat ovens.
Whilst it is approved for direct contact with many food products, packaging made solely from paper and paperboard is permeable to water, water vapour, aqueous solutions and emulsions, organic solvents, fatty substances (except grease resistant paper grades), gases, such as oxygen, carbon dioxide and nitrogen, aggressive chemicals and to volatile flavours and aromas. Whilst it can be sealed with several types of adhesive, it is not itself heat sealable.
Barrier Properties
Paper and paperboard, however, can acquire barrier properties and extended functional performance, such as heat sealability for leak-proof liquid packaging, through coating and lami-nation with plastics, such as polyethylene (PE), polypropylene (PP), polyethylene terephthalate (PET or PETE) and ethylene vinyl alcohol (EVOH), and with aluminium foil, wax, and other treatments.
Packaging made solely from paperboard can provide a wide range of barrier prop-erties by being overwrapped with a heat sealable film, such as polyvinylidene chloride (PVdC) coated-oriented polypropylene (OPP or BOPP) or a similarly coated regenerated cellulose film.
PAPER AND PAPERBOARD – FIBRE SOURCES AND FIBRE SEPARATION (PULPING)
Paper and paperboard are sheet materials comprising an interlaced network of cellulose fibres derived from wood. Cellulose fibres are capable of developing physico-chemical bonds at their points of contact within the fibre network, thus forming a sheet. The strength of the sheet depends on the origin and type of fibre, how the fibre has been processed, the weight per unit area, and thickness.
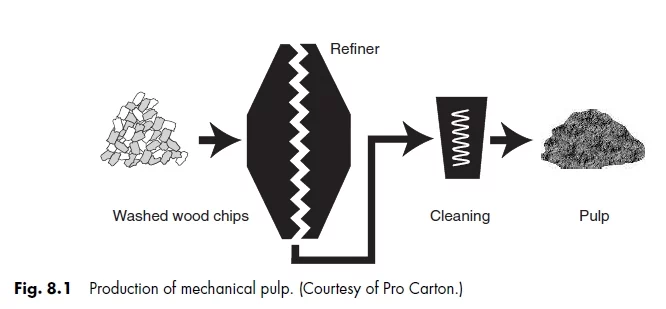
The type of fibre also influences the colour. Most paperboards have a multilayered construction that provides specific performance advantages and gives the manufacturer flexibility of choice, depending on the packaging end use, of the type of fibre used in the individual layers. Virgin, or primary, fibre is derived directly from wood by a process known as pulping. This can be done mechanically (Fig. 8.1) or with the help of chemicals that dissolve most of the non-cellulose components of the wood, which are subsequently used to provide energy (Fig. 8.2).
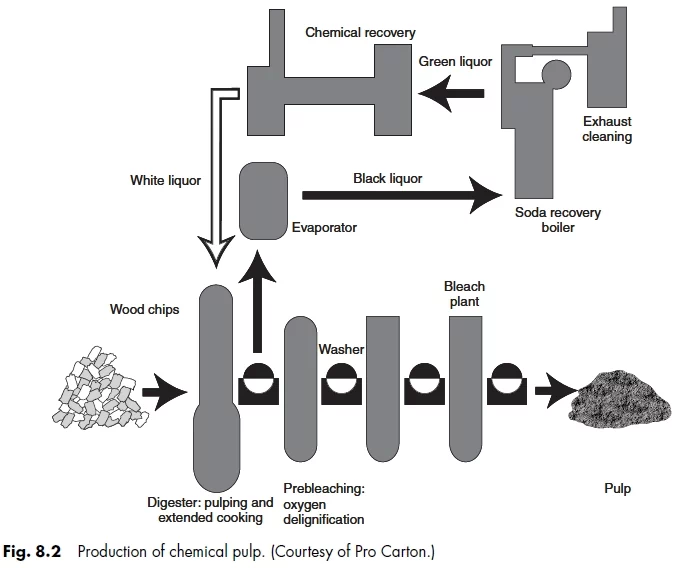
The terms sulphate and sulphite refer to the chemical processes used to separate the fibres from wood, sulphate being the more dominant process today. Mechanically separated fibre retains the colour of the wood though this can be made lighter by mild chemical treatment. Chemically separated fibre is brown but it can be bleached to remove all traces of non-cellulosic material. Pure cellulose fibres are translucent individually but appear white when bulked together (Fig. 8.2).
Fibre recovered (secondary fibre) from waste paper and board, which is not de-inked and bleached, is grey or brown. Fibre recovered from brown packaging will be brown in colour. When mixed printed waste recovered paper and board is processed the colour of the pulp is grey. Pulp can be dyed during processing to meet a specific colour specification. The process whereby recovered fibre is made into paper and paperboard is an example of material recycling (Fig. 8.3).
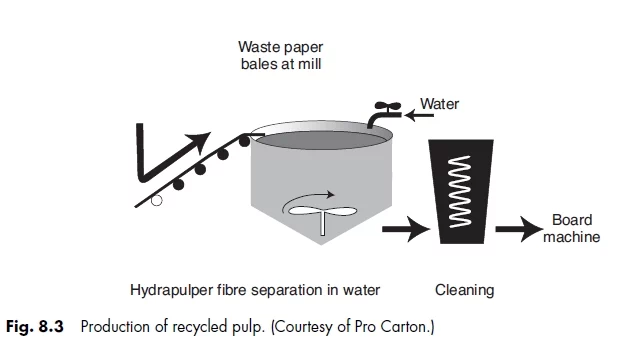
Fibres can withstand multiple recycling but the process of recycling reduces fibre length and inter-fibre bonding, features related to sheet strength properties. Furthermore, it must also be appreciated that some papers and boards cannot be recovered by nature of their use and, hence, there is a constant need for virgin fibre to maintain the amount and strength of fibres. In practice, the proportion of fibre that is recovered and recycled in various countries is between40 and 60%. Another important factor relevant to sheet properties is the species of tree from which the fibres are derived. In general terms, the industry uses long fibres for strength and short fibres for surface smoothness and efficient sheet forming in manufacture. Long fibres are derived from coniferous softwoods, such as Spruce, Pine and Douglas Fir, and have average lengths of 3–4.5 mm. Short fibres, such as those derived from Birch, have average lengths of 1–1.5 mm.
PAPER AND PAPERBOARD MANUFACTURE
Stock preparation
If pulp is bought in bales, it is first dispersed in water in a hydrapulper. All pulp, including pulp that comes straight from the pulpmill without drying, is then treated in various ways to prepare it for use on the paper or paperboard machine. Inter-fibre bonding can be increased by mechanical refining, in which the surface structure of the fibre is modified by swelling the fibre in water and increasing the surface area. The degree of refining, which also influences the drainage rate at the next stage in manufacture, is adjusted to suit the properties of the intended paper or paperboard product.
Additives, such as alum or synthetic resins, are used to increase the water repellancy of the fibres. Wet strength resins can be added to increase the strength of the product when saturated with water. Fluorescent whitening agents (FWAs), also known as optical brightening agents (OBAs), can be added at this stage to increase whiteness and brightness.
Sheet forming
The fibre in water suspension, roughly 2% fibre and 98% water, is formed in an even layer. This is achieved by depositing the suspension of fibre at a constant rate onto a moving plastic mesh, known as the wire (Fig. 8.4). On some machines, forming is carried out on a wire mesh covered cylinder. Forming results in a layer of entangled fibres from which water is then removed by drainage, which may be assisted by vacuum. Tissue, paper, and thin boards can be formed in one layer. Thicker and heavier higher grammage paperboards require several layers of pulp, either the same type, or different pulps, depending on the board type, being brought together successively in the wet state.
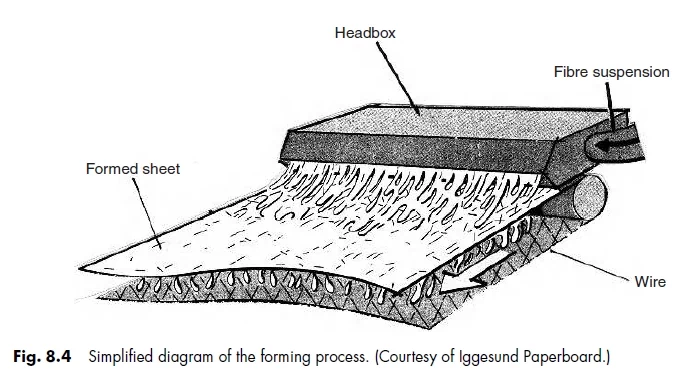
Forming on a wire mesh in this way has two important consequences.
Firstly, there is a slight difference in appearance between the wire side of the sheet and the other side (top side). This effect is eliminated if the sheet is subsequently coated with a white mineral (china clay) coating, or if a specific type of twin wire former is used where both outer sides of the sheet are in contact with identical wire mesh surfaces.
Secondly, the method of forming influences the orientation of the fibres in the sheet. Since fibres are long and thin, they tend to line up in the direction of motion on the machine. This is called the machine direction (MD). Strength properties, such as tensile and stiffness, are higher in the MD. One of the aims of successful forming is to randomise the orientation of fibres in the sheet. Nevertheless, the orientation occurs and it is normal to measure strength properties both in the MD and in the direction at right angles to the MD, known as the cross direction (CD). The fibres form an entangled network that is assisted by creating turbulence in the headbox immediately prior to forming and, on some paper machines, by shaking the wire from side to side.
Pressing
At the end of the forming section, or wet end of the machine, the sheet is sufficiently consolidated by the removal of water to support its own weight to transfer into the press section (Fig. 8.5). Here it is held between absorbent blankets and gently pressed using steel rolls so that with vacuum assistance more water is removed, reducing the moisture content to about 60–65%.

Drying
The moisture is reduced to less than 10%, depending on grade, by passing the sheet over steam heated cylinders. Some machines include in their drying section a very large heated cylinder with a polished steel surface. This is an MG (machine glazing) cylinder – also known as a Yankee cylinder. Paper can be produced with a glazed surface on one side and on some board machines the MG cylinder is used to produce a smooth surface, whilst preserving thickness, thereby giving higher stiffness for a given grammage. A starch solution is sometimes applied towards the end of the drying section to one or both sides of the sheet. This is known as surface sizing. It improves the strength and finish of the sheet and anchors the fibres firmly in the sheet. Squeezing the sheet through a series of steel/composition rolls can enhance smoothness and thickness uniformity. This is known as calendering. Paper may be calendered at high speed in a separate process, known as supercalendering.
Coating
White pigmented coatings are applied to one or both sides of many types of paper and board on- machine. The coatings comprise mineral pigments, such as china clay and calcium carbonate, and synthetic binders (adhesives), dispersed in water. Excess coating is usually applied, it is smoothed and the excess removed. A number of techniques may be used – metering bar, air knife or blade coating.
One, two or three layers of coating may be applied. Coatings are dried by radiant heat and by passing the sheet over steam heated drying cylinders. They may be burnished (polished) depending on the required appearance, colour, smoothness, gloss and printing properties. Coat- ings can be applied off-line. In the cast coating process, the smooth wet coating is cast against a highly polished chromium-plated heated cylinder. When dry, the coating separates from the metal surface leaving the coating with high smoothness and gloss.
Reel-up
Finally, the paper or board is reeled up prior to finishing.
Finishing
The large diameter, full machine width reels of paper and board are then slit into narrower reels of the same or smaller diameter or cut into sheets to meet customer and market needs. Sheets may be guillotined, pile turned, counted, ream wrapped, palletised, labelled and wrapped securely, usually with moisture resistant material, such as PE coated paper or PE film.
PACKAGING PAPERS AND PAPERBOARDS
A wide range of papers and paperboards are commercially available to meet market needs resulting from the choice of fibres available, bleached and unbleached, virgin and recycled, and because fibres can be modified at the stock preparation stage.
Paper and board-based products can be made in a wide range of grammages and thicknesses. The surface finish (appearance) can be varied mechanically. Additives introduced at the stock preparation stage provide special properties.
Coatings applied, smoothed and dried, to either one or both surfaces, offer a variety of appearance and performance features that are enhanced by subsequent printing and conversion, thereby resulting in various types of packaging.
To illustrate these features of paper and paperboard, some examples are described below.
Wet strength paper
Paper sacks used in wet conditions need to retain at least 30% of their dry strength when saturated with water. To achieve wet strength, urea formaldehyde and melamine formaldehyde are added to the stock. These chemicals cross-link during drying and are deposited on the surface of the cellulose fibres making them resistant to water absorption.
Microcreping
Microcreping, e.g. as achieved by the Clupak process, builds an almost invisible crimp into paper during drying enabling paper to stretch up to 7% in the MD compared to a more normal 2%. When used in paper sacks this feature improves the ability of the paper to withstand dynamic stresses, such as occur when sacks are dropped.
Greaseproof
The hydration (refining) of fibres at the stock preparation stage, already described, is taken much further than normal. It is carried out as a batch process and is known as beating. The fibres are treated (hydrated) so that they become almost gelatinous.
Glassine
This is a supercalendered (SC) greaseproof paper. The calendering produces a very dense sheet with a high (smooth and glossy) finish. It is non-porous, greaseproof, can be laminated to board and can be silicone coated to facilitate product release. Glassine is also available in several colours.
Vegetable parchment
Bleached chemical pulp is made into paper conventionally and then passed through a bath of sulphuric acid. Some of the surface cellulose is gelatinised on passing into water and redeposited between the surface fibres forming an impervious layer. This paper has high grease resistance and wet strength.
Tissues
Neutral pH grades with low chloride and sulphate residues are laminated to aluminium foil. The grammages range from 17 to 30 g/m2. Tea and coffee bag tissue is a special light weight tissue available either as a heat sealable product (containing a proportion of polypropylene fibres), or as a non-heat sealable product, in grammages from 12 to 17 g/m2. It incorporates long fibres, such as those derived from manilla hemp, which give a strong permeable sheet at the low grammages used.
A 100% biodegradable and compostable tea and coffee bag tissue is now available with fibre based on IngeoTM (PLA, polylactic acid). This product is suitable for use on tea and coffee, packing machines that use ultrasonic sealing technology (Ahlstrom, 2009).
Paper labels
These may be MG (machine glazed), MF (machine finished) or calendered kraft papers (100% sulphate chemical pulp) in the grammage range 70–90 g/m2. The paper may be coated on- machine or cast coated for the highest gloss in an off-machine or secondary process.
The term finish in the paper industry refers to the surface appearance. This may be:
- MF – machine finish, smooth but not glazed
- WF – water finish where one or both sides are dampened and smoothed, to be smoother and glossier than MF
- MG – machine glazed with high gloss on one side only
- SC – supercalendered, i.e. dampened and polished off-machine to produce a high gloss on both sides
Bag papers
For sugar or flour, coated or uncoated bleached kraft in the range 90–100 g/m2 is used. Imitation kraft is a term on which there is no universally agreed definition, it can be either a blend of kraft with recycled fibre or it can be 100% recycled. It is usually dyed brown. It has many uses for wrapping and for bags where it may have an MG and a ribbed finish. Thinner grades may be used for lamination with aluminium foil and PE for use on form/fill/seal machines.
Sack kraft
Usually, this is unbleached kraft (100% sulphate chemical) pulp, though there is some use of bleached kraft. The grammage range is 70–100 g/m2.
Impregnated papers
Wax impregnated paper and fluorocarbon treatment for grease/fat resistance is produced on- machine.
Laminating papers
These are coated and uncoated papers (40–80 g/m2) based on both kraft (sulphate) and sulphite pulps. These papers can be laminated to aluminium foil and extrusion coated with PE. The heavier weights can be PE laminated to plastic films and wax or glue laminated to unlined chipboard.
Solid bleached board (SBB)
Solid bleached board is made exclusively from bleached chemical pulp (Fig. 8.6). It usually has a mineral pigment coated top surface and some grades are also coated on the back. The term SBS (solid bleached sulphate), derived from the method of pulp production, is sometimes used to describe this product.
This paperboard has excellent surface and printing characteristics. It gives wide scope for innovative structural design and can be embossed, cut, creased, folded and glued with ease.
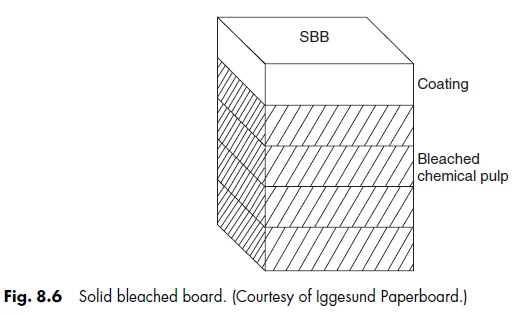
This is a pure cellulose primary (virgin) paperboard with consistent purity for food product safety, making it the best choice for the packaging of aroma and flavour sensitive products. Examples of use include chocolate confectionery, frozen foods, cheese, tea, coffee, reheatable products and as a base for liquid packaging.
Solid unbleached board (SUB)
Solid unbleached board is made exclusively from unbleached chemical pulp (Fig. 8.7). The base board is brown in colour. This product is also known as solid unbleached sulphate. To achieve a white surface, it can be coated with a white mineral pigment coating, sometimes in combination with a layer of bleached white fibres under the coating. This board is used where there is a high strength requirement in terms of puncture and tear resistance and/or good wet strength is required, such as for bottle or can multipacks, and as a base for liquid packaging.
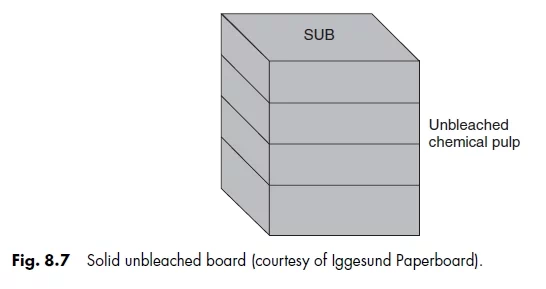
Folding boxboard (FBB)
Folding boxboard comprises middle layers of mechanical pulp sandwiched between layers of bleached chemical pulp (Fig. 8.8). The top layer of bleached chemical pulp is usually coated with a white mineral pigment coating. The back is cream (manilla) in colour. This is because the back layer of bleached chemical pulp is translucent allowing the colour of the middle layers to show through.
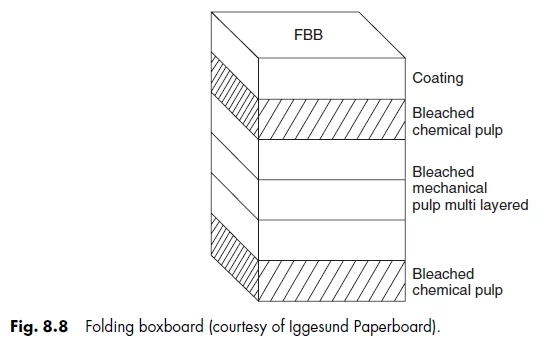
However, if the mechanical pulp in the middle layers has been given a mild chemical treatment (bleached), it is lighter in colour, and this makes the reverse side colour lighter in shade. The back layer may, however, be thicker or coated with a white mineral pigment coating, thus becoming a white back folding box board. The combination of inner layers of mechanical pulp and outer layers of bleached chemical pulp creates a board with high stiffness. Fully coated grades have a smooth surface and excellent printing characteristics. This pa- perboard is a primary (virgin fibre) product with consistent purity for food product safety and suitable for the packing of aroma and flavour sensitive products. It is widely used for food prod- ucts, such as confectionery, frozen and chilled foods, tea, coffee, bakery products and biscuits.
White lined chipboard (WLC)
White lined chipboard comprises middle plies of recycled pulp recovered from mixed papers or carton waste. The middle layers are grey in colour. The top layer, or liner of bleached chemical pulp is usually white mineral pigment coated. The second layer, or under liner, may also comprise bleached chemical pulp or mechanical pulp. This product is also known as newsboard. The term chipboard is also used, though this name is more likely to be associated with an unlined grade, i.e. without a white, or other colour, surface liner ply (Fig. 8.9).
The reverse-side outer layer usually comprises specially selected recycled pulp and is grey in colour. The external appearance may be white by the use of bleached chemical pulp and, possibly, a white mineral pigment coating. (White PE has also been used.) There are additional grades of unlined chipboard and grades with special dyed liner plies for use in the manufacture of corrugated fibreboard.
The overall content of WLC varies from about 80–100% recovered fibre depending on the choice of fibre used in the various layers. WLC is widely used for cereals, dried foods, frozen and chilled foods, and confectionery outers.
PROPERTIES OF PAPER AND PAPERBOARD
The features of paper and paperboard that make these materials suitable for packaging relate to appearance and performance. These features are determined by the type of paper and paper- board – the raw materials used and the way they have been processed.
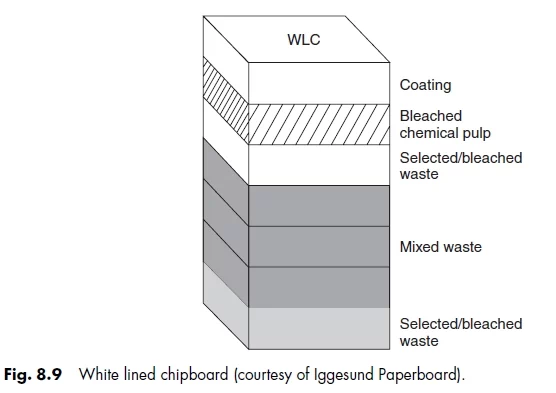
Appearance and performance can be related to measurable properties that are controlled in the selection of raw materials and the manufacturing process.
National and international standard test procedures have been published by British Standards (UK), DIN (Germany), ISO, and in the United States, there is TAPPI (Technical Association for the Pulp and Paper Industry) and ASTM International (formally the American Society for Testing Materials).
Appearance
Appearance relates to the visual impact of the pack and can be expressed in terms of colour, smoothness and whether the surface has a high or low gloss (matte) finish.
Colour depends on the choice of fibre for the outer surface, and also, where appropriate, the reverse side. As described above, the choice is either white, brown or grey. In addition, some liners for corrugated board comprise a mix of bleached and brown fibres.
Other colours are technically possible either by using fibres dyed to a specific colour or coated with a mineral pigment-coloured coating. Where paper and paperboard is required for quality printing, it is usually coated on the print side during manufacture with a mineral-based coating, usually white in colour, based on china clay or calcium carbonate. The reverse side may also be coated where two-side printing is required.
Performance
Performance properties are related to the level of efficiency achieved during the manufacture of the pack, in printing, cutting and creasing, gluing and the packing operation. Performance properties are also related to pack compression strength in storage, distribution, at the point of sale and in consumer use.
Specific measurable properties include stiffness, short span compression (rigidity) strength, tensile strength, wet strength, % stretch, tear strength, fold endurance, puncture resistance and ply bond strength. Other performance properties relate to moisture content, air permeability, water absorbency, surface friction, surface tension, ink absorbency, etc. Chemical properties include pH, whilst chloride and sulphate residues are relevant for aluminium foil lamination.
Flatness is easily evaluated but is a complicated issue as lack of flatness can arise from several potential causes, from the hygrosensitivity characteristics of the fibre, manufacturing variables and handling at any stage, including printing and use. Neutrality with respect to odour and taint, and product safety are performance needs that are important in the context of paper and board packaging, which is in direct or close proximity to food.
ADDITIONAL FUNCTIONAL PROPERTIES OF PAPER AND PAPERBOARD
Additional barrier and functional performance for food packaging needs can be imparted to paper and paperboard by one or more of the following processes.
Treatment during manufacture
- Hard sizing
Sizing is a term used to describe a treatment that delays the rate at which water is absorbed, both through the edges (wicking) and through the surface. It is achieved by the use of chemicals added during the stock, or pulp, preparation stage prior to forming in manufacture. This is known as internal sizing. Traditionally, alum, a natural resin, derived from wood was used. Today several synthetic sizing materials are also available. Paperboard used in packaging for frozen and chilled food and for liquid packaging needs to be hard sized.
- Sizing with wax
Sizing with wax on-machine.
- Acrylic resin dispersion
Acrylic resin dispersion (water-based) coating – heat sealable, moderate moisture and oxygen barrier, available as one side coating on-machine.
- Fluorocarbon dispersion
Fluorocarbon dispersion coating, high fat resistant one-side coating on-machine.
Note: The terms on-machine and off-machine are commonly used in the paper industry. The machine in question is the paper or paperboard machine. An on-machine process takes place as the paper or paperboard is being made and off-machine is a subsequent process carried out on a machine designed specially for the process concerned.
Lamination
This process applies another functional or decorative material, in sheet or reel form, to the paper or paperboard surface with the help of an adhesive. Examples are:
- aluminium foil applied to one or both sides, provides a barrier to moisture, flavour, common gases, such as oxygen, and UV light. Aluminium foil laminated to paper and paperboard is also used for direct contact and easy release for foods that will be cooked or reheated in radiation or convection ovens. Aluminium foil is also used to provide a decorative metallic finish as, for example, on cartons for chocolate confectionery
- greaseproof paper laminated to paperboard: good grease resistance for fat containing prod- ucts, temperature resistance to 180◦C for cooking/reheatable packs. If additionally the grease- proof paper has a release coating, this product can be used to pack sticky or tacky products
- glassine paper laminated to paperboard: grease resistance for products with moderate fat content, such as cakes or bake-in-box applications. If the glassine is coloured the pack should not be used in reheatable applications but food contact approved grades can be used for direct contact with, for example, chocolate
The adhesives used for lamination include PVA-type emulsions, starch-based, resin/solvent- based, cross-linking compounds, molten wax or PE depending on the needs of the particular laminate. The presence of wax and PE also improves the barrier to water vapour. When PE is used as an adhesive the process would be described as extrusion lamination.
Plastic extrusion coating and laminating
Polyethylene (PE) heat sealable moisture barrier. Low density polyethylene (LDPE) is widely used in the plastic extrusion coating and laminating of paper and paperboard. Easier heat sealing results when PE is modified with EVA (Ethylene vinyl acetate). Medium and high density PE has a higher temperature limit, better abrasion resistance and higher barrier properties than LDPE. One and two side coatings are available (Fig. 8.10).
Polypropylene (PP) heat sealable, moisture and fat barrier. It can withstand temperatures up to 140◦C and is used for packing foods to be reheated in ovens up to this temperature. One and two side coatings are available.
Polyethylene terephthalate (PET) heat sealable, moisture and fat barrier. It can withstand temperatures up to 200◦C and is dual ovenable (microwave and conventional ovens). It is coated only on the non-printing side.
Polymethylpentene (PMP) moisture and fat barrier and not heat sealable. It is, therefore, used as flat sheets, deep drawn trays and trays with mechanically locked corners. It is coated only on the non-printing side.
Ethylene vinyl alcohol (EVOH) and polyamide (PA) heat sealable, fat, oxygen and light barrier. EVOH is moisture sensitive and needs to be sandwiched between hydrophobic materials, such as PE. It can be used as a non-metallic alternative to the aluminium foil layer.
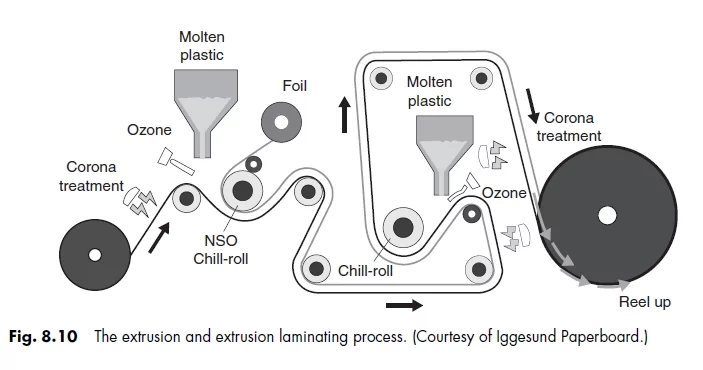
Ionomer resin (SurlynQR ), a polyolefin with high resistance to fat, including essential oils in citrus fruit, and moisture with very good sealing properties, is used as a tie layer on aluminium foil when applying PE to foil.
Bioplastic extrusion coatings are now available as a PE alternative. This starch-based material is sustainable and meets the EN13432 standard for compostability (Packaging News 2008).
The process of extrusion is often extended to include extrusion lamination so that a structure, such as paper or paperboard/PE/aluminium foil/PE, can be produced in one operation on an extruder with two extruding units.
Note: By special selection of polymers, e.g. for lids and trays, it is possible to provide easy-open peelable heat-seals.
Printing and varnishing
Usually, printing and varnishing are associated with the appearance of the pack with respect to the visual impact of the pack through colour, information, text and illustration. There are also important functional aspects of printing and varnishing that are important for food packaging.
All the main printing processes are used – gravure, flexographic, letterpress, silk screen and lithographic. Paper and paperboard can also be printed by the recently introduced digital process. Choice is influenced by the appearance and performance (functional) needs and commercial aspects, such as order size, lead time and price.
The inks and varnishes may be those described as traditional for the process concerned, based on pigment, resin and vehicle. The vehicle, which transports the pigment and resin from the ink or varnish reservoir to the substrate via the printing plate, varnish pick-up roll, etc., may be an organic solvent, water or a drying oil. For some processes, pigments are replaced by dyes. In recent years, inks and varnishes cured by UV radiation have also become popular, and these materials are extremely inert. They give good rub resistance in wet and dry conditions and are resistant to product absorption. The inks contain pigment, cross-linking resins and a photo-initiator; they are 100% solid and are dry immediately after printing.
The functional requirements include adherence to colour standards, light fastness, rub re- sistance, print-to-print and print-to-pack registration and stability within the conditions of use. For some food products where the print is in close proximity to the food, e.g. chocolate con- fectionery, it is important that no residual solvents from the inks and varnishes, or any other interaction between print and product affects the food product.
Post-printing roller varnishing/coating/laminating
Post-printing roller varnishing and coating is usually associated with high gloss and can involve UV cured varnishes. The process can also be used for the application of functional varnishes to meet specific end use needs. The most common example of this is the application of heat-seal coatings for blister packs.
Another example of coating is the application of wax. This can take a variety of forms:
- dry waxing where molten wax is applied to one or both sides of a printed paper or a printed/cut/creased carton blank. The appearance is a matte finish
- wet or high gloss waxing. Immediately after coating, the printed paper or carton blank is conveyed through very cold water. This causes the wax to set immediately, producing a very high gloss finish
Waxed paperboard provides water and water vapour resistance. It can be heat sealable. The first liquid packaging cartons (∼1920) were waxed. Wax is also a good gas barrier and can therefore protect food products against flavour loss or ingress of contamination. The main food applications today are for bread wrap, items of sugar confectionery (paper), frozen food and ice cream (cartons) and fresh produce (corrugated board). Cellulose acetate and OPP laminated to paperboard enhance appearance after printing.
DESIGN FOR PAPER AND PAPERBOARD PACKAGING
Surface design concerns colour, text, illustrations, decoration, finish (gloss or matte) and surface texture. It is achieved by making use of the basic surface properties of the paper or paperboard and through lamination, coating, hot foil stamping, embossing, printing and varnishing. Surface design usually refers to the external surface of a pack but there are situations where the internal surface is important for the overall effect, e.g. the inside surfaces of chocolate and tea bag cartons. Structural design is concerned with the shape of packages. The functional shape is determined by the needs of the pack, e.g. closure and opening features. Creative shape adds interest for promotional needs where that is appropriate. Paper and paperboard are materials that give a designer freedom to develop imaginative solutions in meeting customer needs. This is due to a number of factors:
- range of surfaces, in terms of colour and finish, available
- range of strength properties, in terms of fibre type, thickness and method of manufacture, available
- choice of functional coating, lamination, decoration, printing, etc
- ease of conversion into packages in terms of cutting, creasing, folding, gluing, locking, heat sealing, etc
- innovative machinery for conversion and packing