The max grammage an offset press can handle is no more than 400gsm, which is around 0.50-0.55mm. Then how to get a 700gsm paperboard printed to get a very thick black paper box? Recently a client in UK asked us to make such a custom paper box for the coffee packaging. Beside the custom thickness, debossing and embossing finish are both used onto the box.
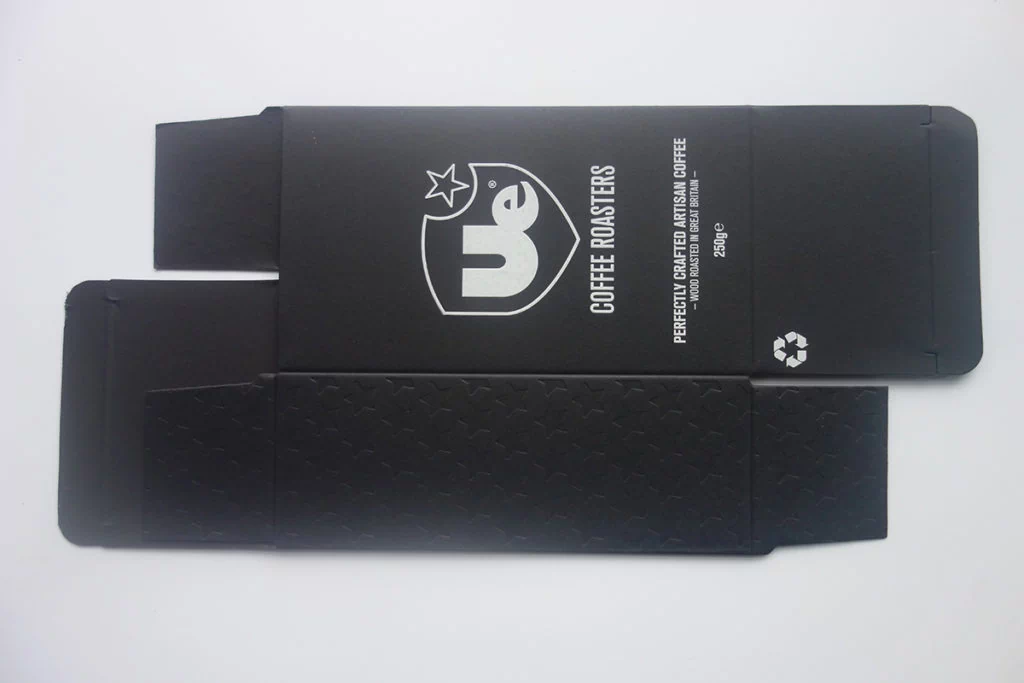
The F flute corrugated box is an option. The crisp full color printing of the F flute, E flute box is achieved through the litho laminating process in which a piece of 300gsm CCNB paperboard is glued onto the single faced corrugated board. But the fluting paper sometimes give some customers a sense of cheap quality, even though it is not always the truth. The corrugated box can high-end and luxury.
The 700gsm paperboard is around 0.7-0.8mm in thickness. No litho press can handle such a piece of thick paperboard. Screen silk printing is a solution, but it lacks accuracy and precision. Then how do we solve the problem?
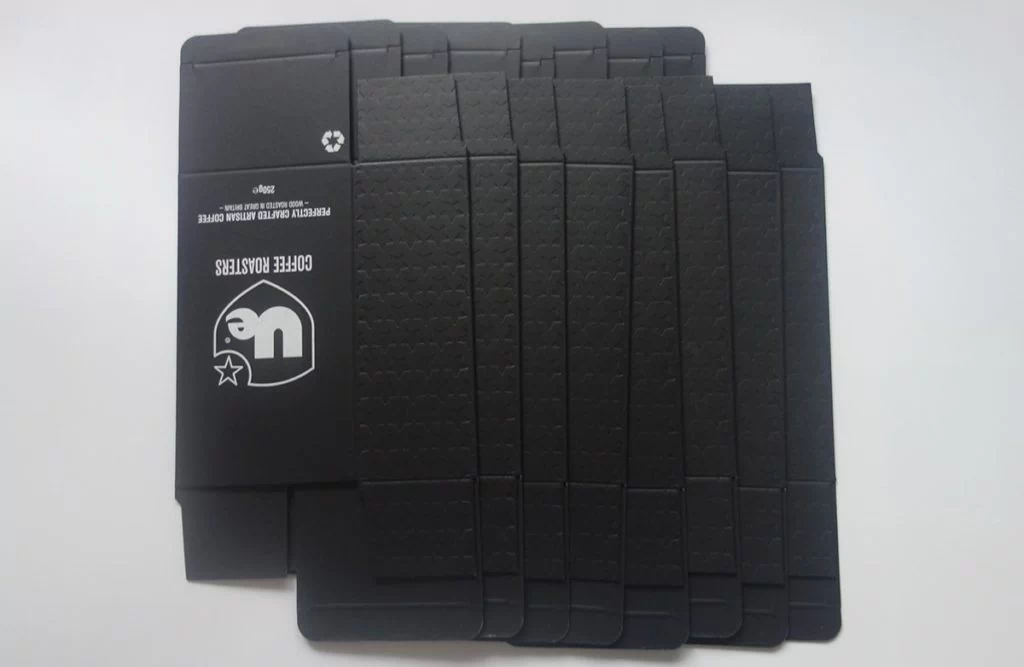
Here is the secret. The process is much the same as the litho laminating for the corrugated boxes. We have 2 piece of 350gsm black specialty paperboard and glue them together. Firstly, we do the litho printing on one piece of 350gsm black specialty paper, then we glue it to the other piece of the black specialty paperboard.
Besides the thickness of the box, the client has some other special requirement, debossing for the star patterns on the left side and right side panels of the box, embossing for the logo image on the front panel.
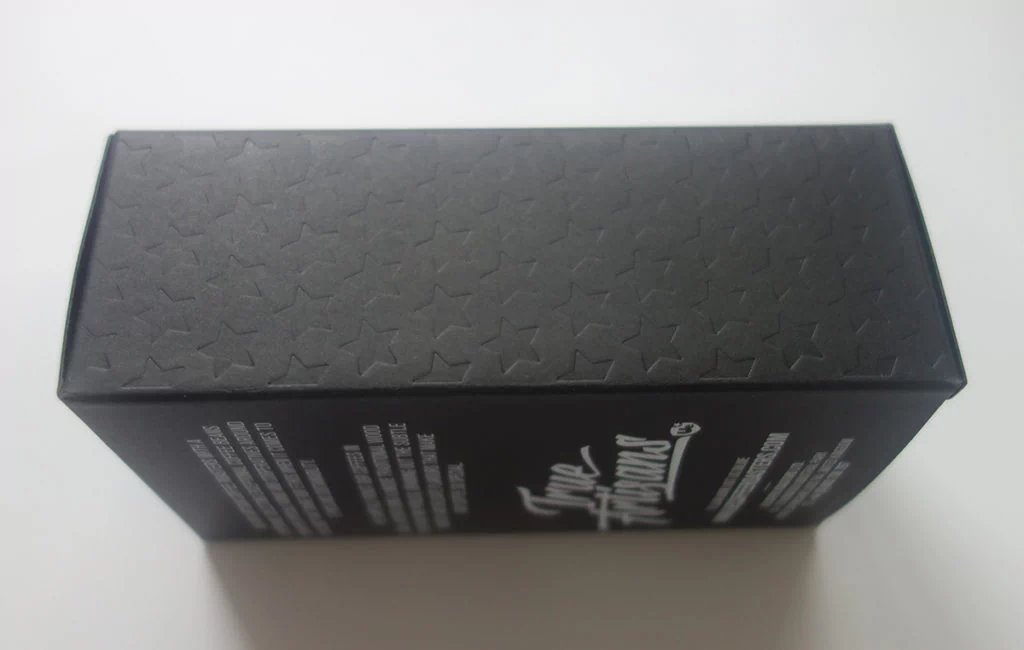
Other features of the coffee paper box includes the STE box structure, which is referred to as the straight tuck end paper box. For the color printing, it is the pantone white inks used.